To build better lithium-ion batteries, scientists are using advanced imaging and analysis tools to fine-tune battery materials.
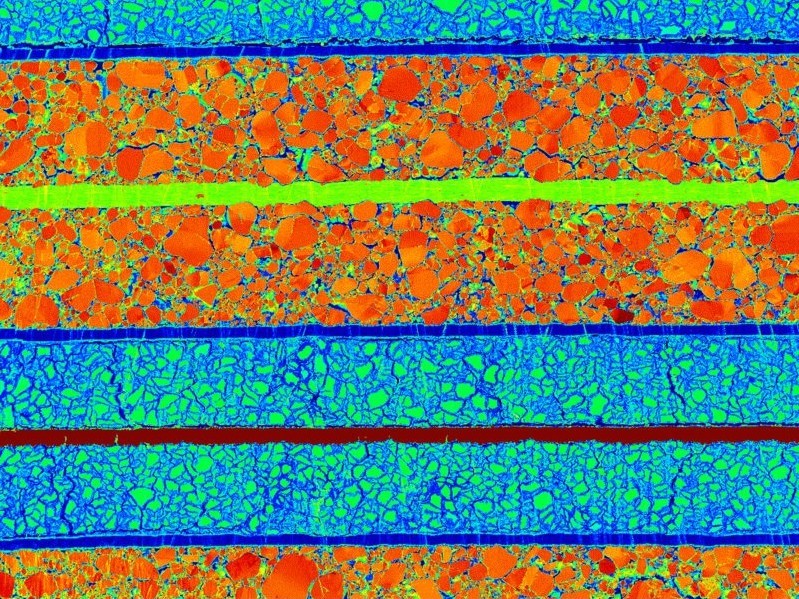
New sample analysis and visualization tools are yielding clear images of what happens when lithium-ion batteries charge and discharge, such as this 250X scanning electron micrograph of a sample created using a cryo-cooled cross-section polisher.
Demand for rechargeable batteries is soaring, driven by electric vehicles, renewable energy storage, and portable electronics. Lithium-ion batteries attract the most attention because of their combination of longevity, rechargeability and low cost. Yet today’s lithium-ion systems are far from perfect — just ask anyone whose mobile phone died by mid-afternoon, or whose electric car took hours to recharge.
Tomorrow’s batteries will have to do better, and that presents a challenge. “People want to have batteries with longer cycle life. We want higher energy density. We want higher capacity,” says Grace Gorman, senior director for characterization and failure analysis at Enovix, a company in Fremont, California, that’s developing new batteries for a variety of uses.
Researchers have many potential ways to improve lithium-ion battery performance, ranging from new materials for electrodes to replacing liquid with solid electrolytes. But developing high-performing batteries means understanding lithium’s behavior inside them, and lithium has been loath to give up its secrets. Thanks to new imaging and analysis techniques, however, researchers are learning more about how the lightest of metals behaves in complex battery systems.
Replacement anodes
Whether it’s an iPhone, a laptop, or a car drawing power, what happens in a lithium-ion battery that’s discharging is similar to what happens in the familiar AA battery that has been powering devices for years. Positively charged ions move from the anode to the cathode through an electrolyte — a substance that allows the flow of charge. In lithium-ion batteries, positively charged lithium ions move from anode to cathode through a solution of lithium salts in a mixture of organic solvents. At the same time, electrons from the anode pass to the cathode through the laptop or whatever is drawing power, completing the circuit. When the battery is charging, the process reverses.
In most of today’s lithium-ion batteries, the anode is made of graphite, a heat-resistant, crystalline form of carbon that can store lithium ions. The cathode consists of a lithium-containing compound, such as lithium cobalt oxide. Since lithium is the lightest metal and the third-lightest element, after hydrogen and helium, a lithium-ion battery can store 50% more energy per unit weight than older rechargeable battery chemistries that use heavier metals, such as nickel-cadmium or nickel-metal hydride batteries.
The Enovix team is one of many that seek to increase energy density further by replacing the graphite anode with silicon, which can hold approximately 10 times as many lithium ions as graphite. This would offer a boost of between 15 and 30%, depending on the anode’s design.
Such gains, however, come at a price: anodes expand as they absorb lithium ions, and as they move through charge-discharge cycles, this swelling generates mechanical forces that crack and degrade the anodes over time. But while graphite expands by about 10%, silicon anodes can quadruple in size, making them more vulnerable to degradation.
Visualizing lithium
Battery performance also depends on how lithium ions move through the electrolyte, and where precisely lithium ions sit within the cathode and anode. For that reason, battery makers seek detailed information about lithium’s behavior so they can fine-tune the device’s microstructure.
Enovix’s researchers do this by imaging samples of a battery system at different points during the charge-discharge cycle. But here lithium’s small size becomes a disadvantage. Techniques for localizing atoms often rely on measuring how x-rays scatter as they interact with the electrons of a material. With just three electrons, lithium does not scatter X-rays as strongly as heavier atoms, and those scattered X-rays have very low energy, causing the signal they produce to be drowned out by stronger signals from other materials in the battery.
“It's always a challenge to figure out where the lithium is,” Gorman says. “Lithium is very hard to detect, and a lot of techniques struggle with either the spatial resolution or the quantity.”
What’s more, the same X-rays that visualize lithium ions can also knock lithium and other atoms out of place, damaging the battery material. To avoid this, Enovix researchers combine two techniques that together cause less damage and help find the hidden lithium.
The first method, called soft X-ray emission spectroscopy (SXES), uses X-rays that have longer wavelengths than conventional, or hard, X-rays and are less energetic. These soft X-rays do not illuminate a material’s atoms as intensely as hard X-rays, reducing the background noise in SXES. This makes it easier for researchers to observe the weak lithium signal, says Patrick Phillips, assistant product manager for transmission electron microscopy at JEOL USA, a manufacturer of electron microscopes and other analytical instruments, including the soft X-ray spectrometer that Gorman used.
The second method, called optimum bright-field imaging, was developed at the University of Tokyo and commercialized by JEOL. It uses a modified X-ray detector that separately visualizes images obtained using different X-ray frequencies and recombines them into a high-resolution image. This lowers the overall X-ray dose, protecting the material, while improving the signal-to-noise ratio.
“The [optimum bright-field] imaging technique allows the researchers to look at a sample and to pick out exactly where the lithium atoms are,” says Tom Isabell, a materials scientist and vice president at JEOL.
Air-free analysis
Lithium-ion batteries are typically closed systems that react when exposed to air. To spot atoms of lithium and other elements in experimental batteries, Yan Yao, a materials scientist at the University of Houston, studies samples from batteries in an air-free environment.
Yao is experimenting with different battery chemistries, such as replacing the transition metals used in cathodes with organic materials, which are cheaper and more readily available. To test each battery, he charges and discharges it, while watching how its materials change. He prepares samples with a JEOL ion-beam cross-section polisher that slices through various layers of the battery, leaving an even surface without imperfections. Then he uses a special sample holder he designed to move the sample from, say, a scanning electron microscope to a transmission electron microscope, without exposing it to air.
Yao is also working on devices made with solid, rather than liquid, electrolytes. He has observed how defects along the interface between the electrode and the solid electrolyte develop cracks as the electrode expands and contracts. This causes lithium atoms to form finger-like crystalline growths called dendrites that eventually grow large enough to short-circuit the device. Visualizing dendrite growth is critical to understanding the failure mechanisms that researchers must address. “It’s very hard to predict where the cell will fail,” Yao says. “But now, with this tool, we actually are able to pinpoint the source of the failure.”
And when it comes to understanding battery materials, imaging tools that predict failure may be the key to success. “These detectors are becoming faster,” JEOL’s Phillips says. “The cameras are getting better. Almost every aspect of the research is improving constantly.”
To learn more about imaging methods that are fueling advanced battery research, click here.